Plastic extrusion for thermoplastics, PVC, and engineering plastics
Plastic extrusion for thermoplastics, PVC, and engineering plastics
Blog Article
Recognizing the Essentials and Applications of Plastic Extrusion in Modern Manufacturing
In the world of modern-day manufacturing, the method of plastic extrusion plays a crucial role. Untangling the principles of this process reveals the true flexibility and capacity of plastic extrusion.
The Principles of Plastic Extrusion Process
While it might appear complex, the basics of the plastic extrusion procedure are based upon reasonably straightforward concepts. It is a manufacturing process where plastic is thawed and after that shaped into a continual profile with a die. The raw plastic material, frequently in the form of pellets, is fed into an extruder. Inside the extruder, the plastic is subjected to warmth and pressure, causing it to melt. The liquified plastic is then forced through a shaped opening, recognized as a die, to form a long, continuous item. The extruded item is cooled and after that reduced to the desired length. The plastic extrusion procedure is extensively used in various industries as a result of its cost-effectiveness, performance, and versatility.
Different Kinds Of Plastic Extrusion Strategies
Structure upon the fundamental understanding of the plastic extrusion process, it is required to check out the different methods entailed in this production technique. In comparison, sheet extrusion creates large, level sheets of plastic, which are normally more refined right into items such as food packaging, shower drapes, and car components. Understanding these strategies is crucial to using plastic extrusion efficiently in modern production.
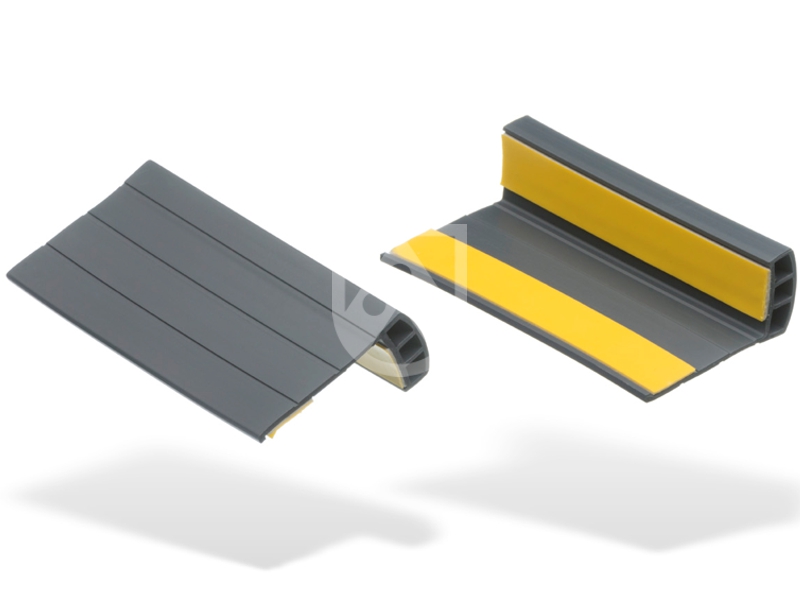
The Role of Plastic Extrusion in the Automotive Sector
An overwhelming majority of components in modern lorries are items of the plastic extrusion procedure. Plastic extrusion is largely used in the production of different car parts such as bumpers, grills, door panels, and control panel trim. Thus, plastic extrusion plays an essential role in vehicle manufacturing.
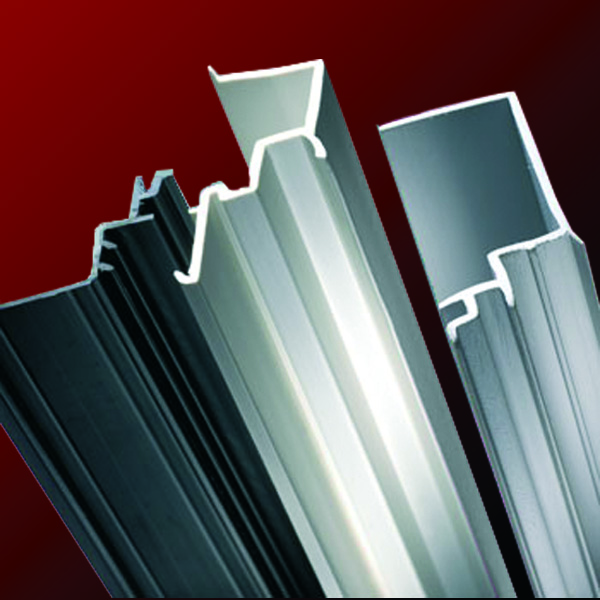
Applications of Plastic Extrusion in Customer Product Manufacturing
Beyond its significant influence on the automobile market, plastic extrusion proves just as efficient in the world of durable goods making. This procedure is crucial in developing a broad selection of items, from food packaging to family home appliances, playthings, and even clinical gadgets. The versatility useful link of plastic extrusion allows suppliers to design and produce complex sizes and shapes with high precision and effectiveness. Due to the recyclability of several plastics, squeezed out components can be reprocessed, lowering waste and cost (plastic extrusion). The versatility, versatility, and cost-effectiveness of plastic extrusion make it a recommended selection for many durable goods makers, adding considerably to the industry's development and that site development. The environmental ramifications of this widespread usage require mindful factor to consider, a subject to be talked about better in the succeeding area.
Environmental Impact and Sustainability in Plastic Extrusion
The prevalent usage of plastic extrusion in manufacturing welcomes scrutiny of its ecological effects. Reliable machinery decreases power usage, while waste management systems reuse scrap plastic, reducing raw product demands. Despite Full Article these improvements, better technology is required to mitigate the ecological impact of plastic extrusion.
Conclusion
In verdict, plastic extrusion plays an essential function in contemporary production, particularly in the automotive and consumer goods fields. Comprehending the fundamentals of this process is essential to enhancing its benefits and applications.

The plastic extrusion procedure is thoroughly utilized in various industries due to its adaptability, cost-effectiveness, and efficiency.
Building upon the fundamental understanding of the plastic extrusion process, it is necessary to check out the numerous methods involved in this production method. plastic extrusion. In contrast, sheet extrusion produces large, flat sheets of plastic, which are generally further processed into items such as food product packaging, shower drapes, and vehicle parts.An overwhelming majority of components in modern cars are products of the plastic extrusion process
Report this page